The Flexible Filament Doser makes it easier to print soft, flexible filaments on conventional FDM 3D printers.
I developed the FFD (Flexible Filament Doser) to make it easier to 3D print with flexible filaments, especially those softer than 75A shore hardness. In developing the flexible wristband for BREW, a wearable haptic feedback device, I sought to use a skin-safe filament that was soft enough to stretch and compress with the device, but strong enough to withstand repeated cycles. For that reason, I chose NinjaTek Chinchilla TPE (Shore hardness: 75A), which is tested to be skin-safe using the EpiDerm skin model.
However, this filament is notoriously difficult to print, even with direct-drive printers such as the Original Prusa MK4S. The filament’s viscoelastic properties make it prone to stretching under tension. This means that it can stretch instead of rotating freely out of the spool, which alters its diameter. As a workaround, we were pulling a handful of filament from the spool at a time, which was a tedious and messy approach - especially for long prints.
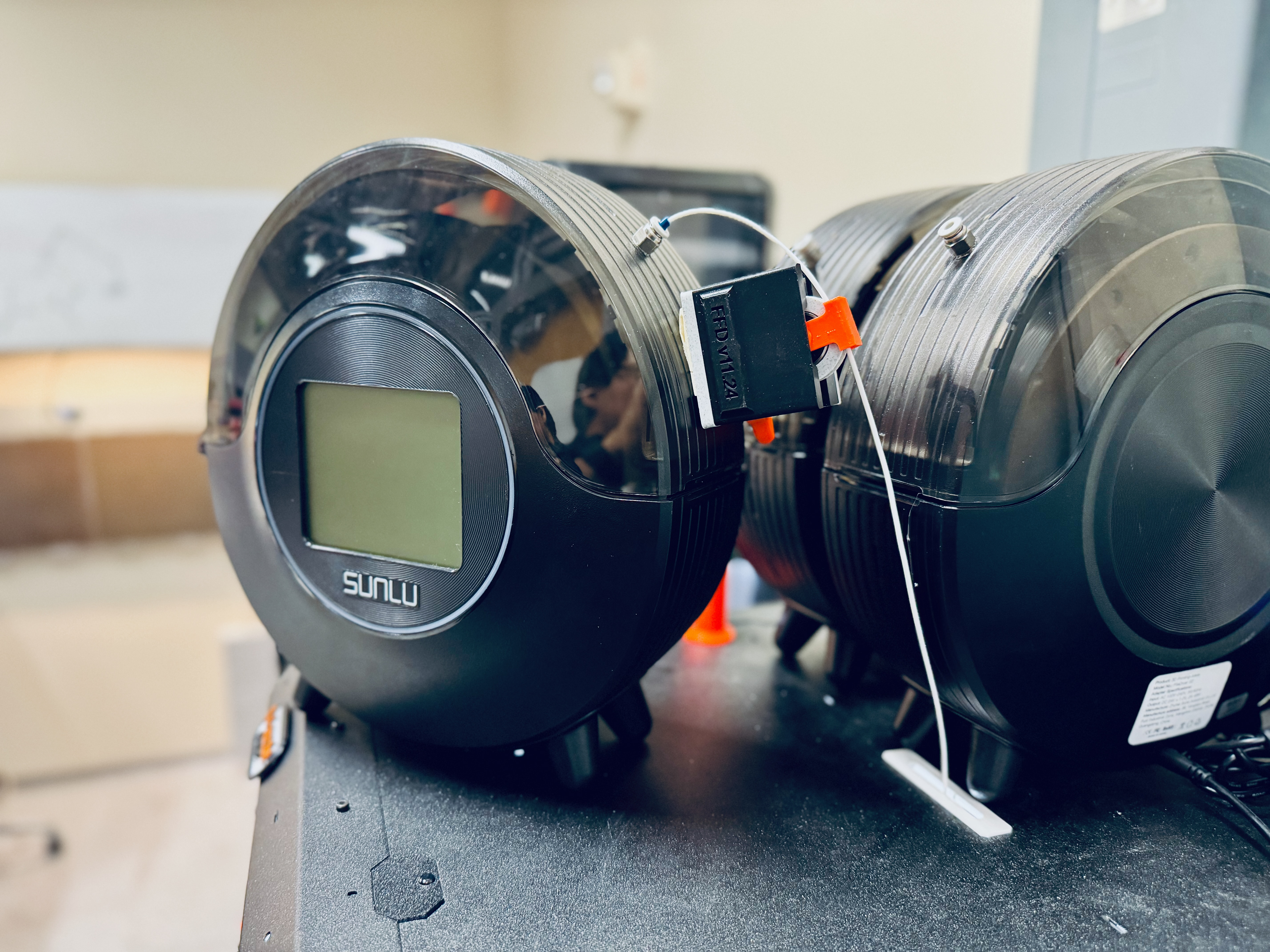
These limitations were the motivation for developing FFD, which attaches anywhere on the filament entry to the printer. This means you can leave your flexible filament in a dry box as it prints, and route the filament through the FFD - critical for moisture-sensitive filaments like Chinchilla TPE.
The FFD module, consisting of a roller and magnet on a spring-loaded linear guide, is pushed down by any excessive tension on the filament. If this occurs, a hall effect sensor in the FFD housing detects the new position of the roller assembly and sends a signal to a DC motor to rotate the filament spool. In this way, the filament tension is eased and the direct driver extruder can print the filament more easily.
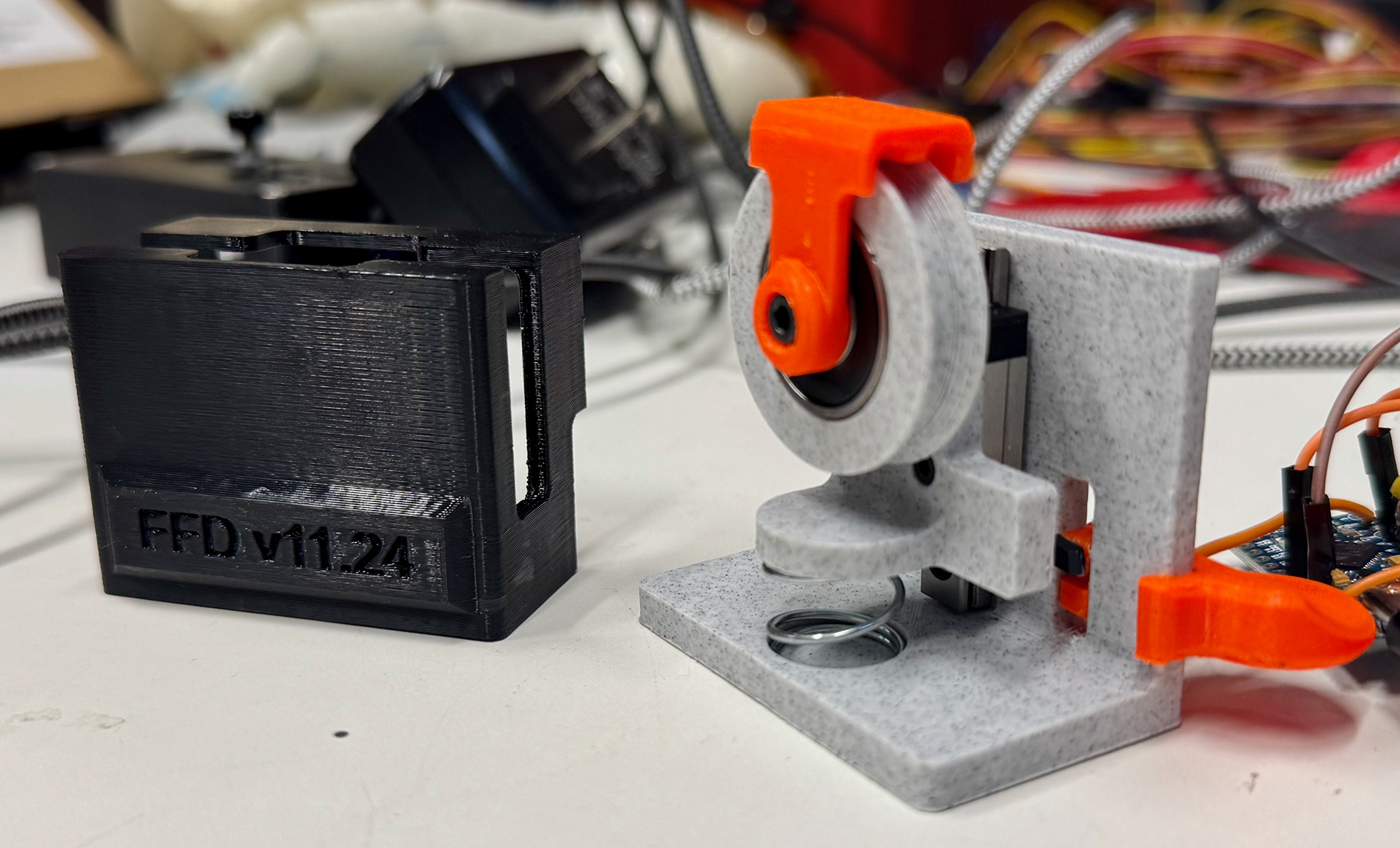
Although I came up with the original idea and prototype, FFD is currently in further development by Yensabro Kanashiro and Ariana Diaz.